
PROFINET is one of the many industrial ethernet systems out there, which is often compared to PROFIBUS.
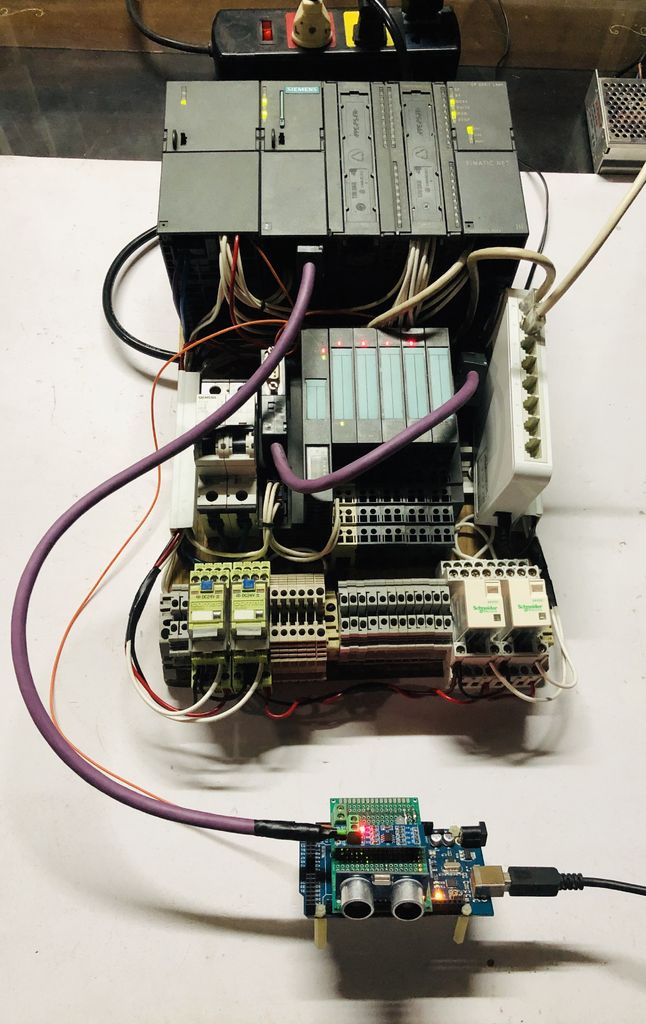
PROFINET is a fieldbus system which is based on Ethernet. PROFIBUS PA can either be wired as a daisy chain or as a star topology, but by using intelligent/advanced junction boxes, PROFIBUS PA can also be installed as a ring topology. PROFIBUS DP networks are most commonly installed as a large daisy chain, creating a fault sensitive network. PROFIBUS DP is based on the RS485 protocol and PROFIBUS PA is based on the MBP-IS protocol, which is a bus-powered protocol. PROFIBUS communication is half duplex, which means that only one device is communicating at the time. PROFIBUS PA runs at a fixed transmission speed of 31.25 kbps, where PROFIBUS DP can be configured to run at a maximum speed of 12 Mbps. PROFIBUS PA (Process Automation) is mostly used in industries such as water treatment, oil, gas, chemicals, etc.
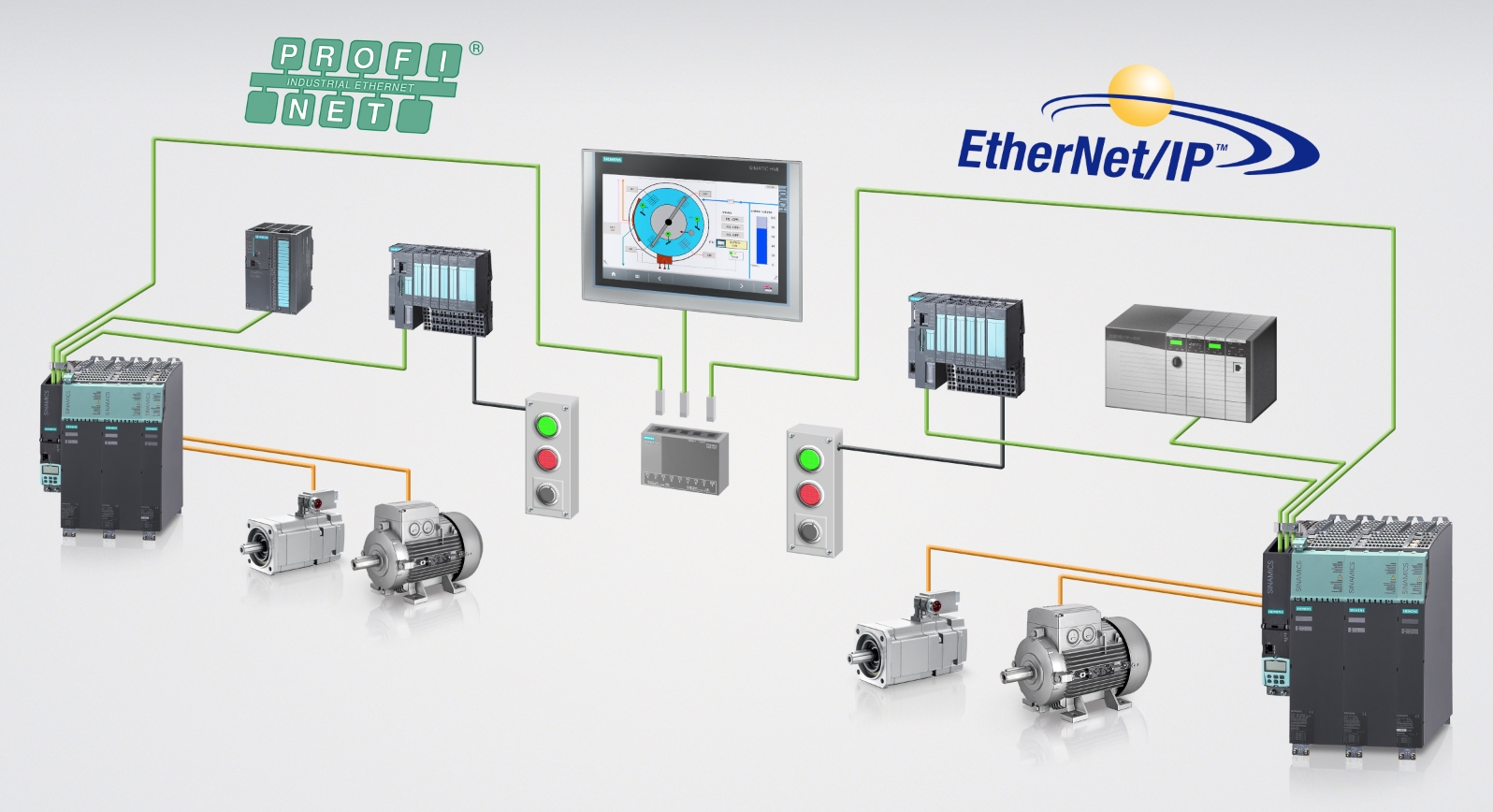
PROFIBUS DP (Decentralized Peripherals) is the high-speed version, which is mostly used for factory automation (i.e. PROFIBUS has two different applications:įor each application PROFIBUS can use a different protocol. PROFIBUS (Process Field Bus) is a fieldbus which is being used for high speed cyclic data communication in the world of automation. Find out below about the main differences. However, their functionalities and features are completely different. PROFIBUS and PROFINET are often compared and indeed share some similarities. It is one of the secure methods of data transfer where connection can be established and terminated from both Local & Partner PLC using TCON & TDISCON instructions.PROFIBUS vs PROFINET: what are the main differences? We studied one of the methods to establish communication between PLC’s using TSEND & TRCV instructions in Open User Connection. We can share a large amount of data compared to GET & PUT Instructions.It is a secure method of data exchange between devices.Change the parameter REQ to “TRUE” for CPU_1.When the connection is established by TCON, the TSEND instruction shall send the data based on the Input Parameter ID.Īt the same time, the TRCV instruction shall receive the data based on the Input Parameter ID.įor Terminating Connection (TDISCON), observe the output by making the following changes. Change the parameter REQ to “TRUE” for CPU_2.The below steps explains the procedure to do the PLC to PLC data transfer and receive using the open user communication method in Tia Portal.ĭrag two CPU’s from TIA Catalog into Hardware Configuration of TIA Portal.įor Establishing Connection (TCON), observe the output by making the following changes. Open User Communication Configuration Steps The medium used is Profinet / Industrial Ethernet. The above instructions use TCP protocol for data transfer. Using above instructions we can establish communication between PLC and any other Active / Passive Device. TRCV – Receive Data via Communication Connection.TSEND – Send Data via Communication Connection.TDISCON – Terminate Communication Connection.TCON – Establish Communication Connection.
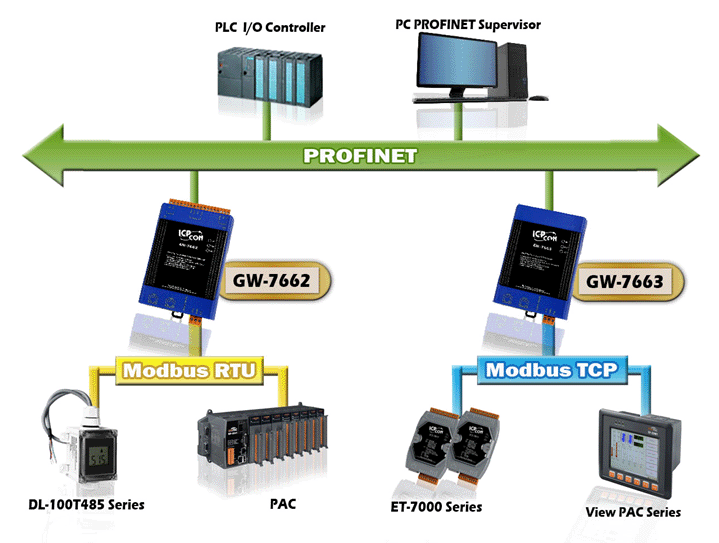
The instructions that come under this method are listed below. The communication between devices with different make & model is established using a method called “ Open User Communication“. In Siemens TIA Portal, there are multiple ways of establishing communication between active or passive devices.
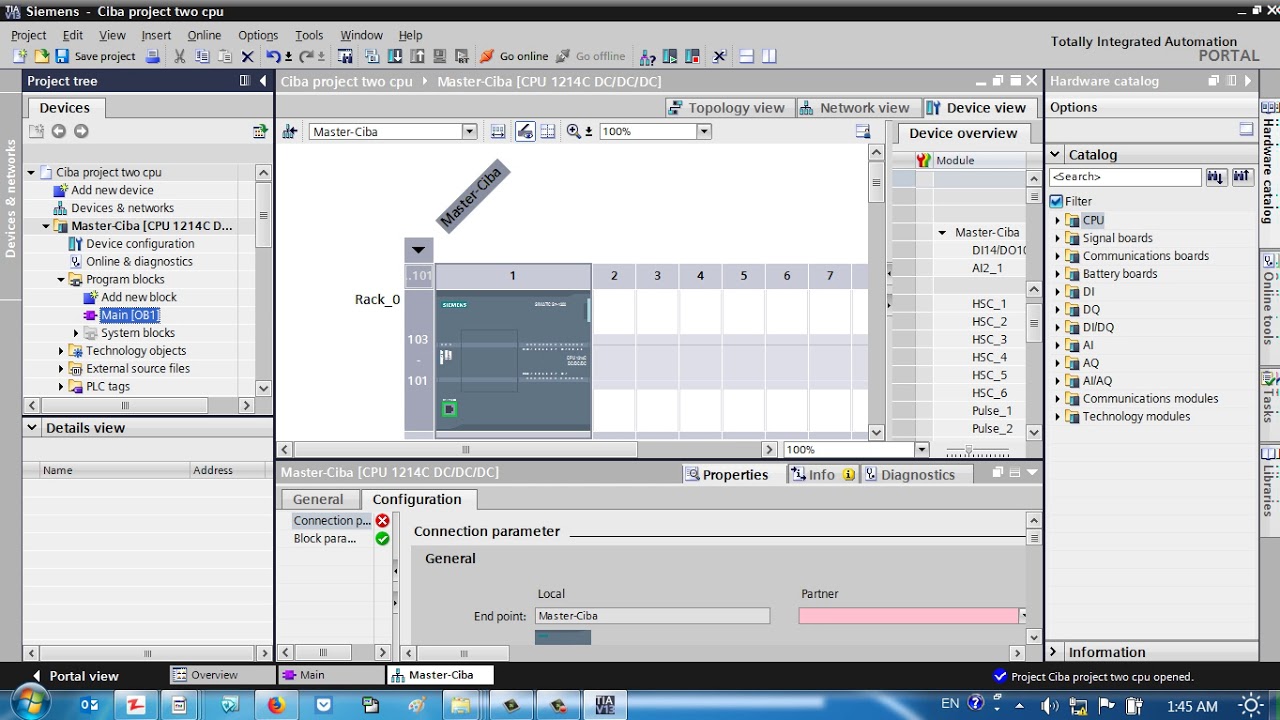
In this article, we discuss the PLC to PLC communication using open user communication in Siemens Tia Portal.
