
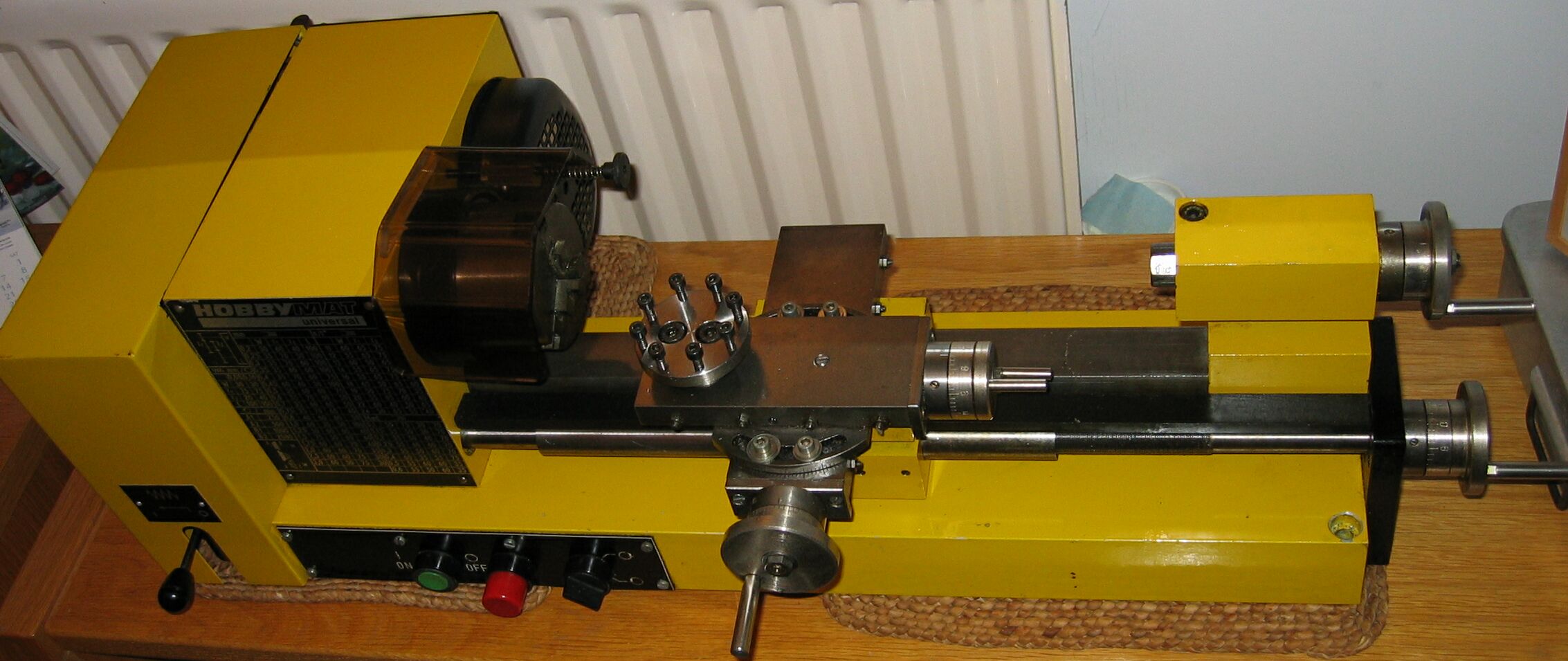
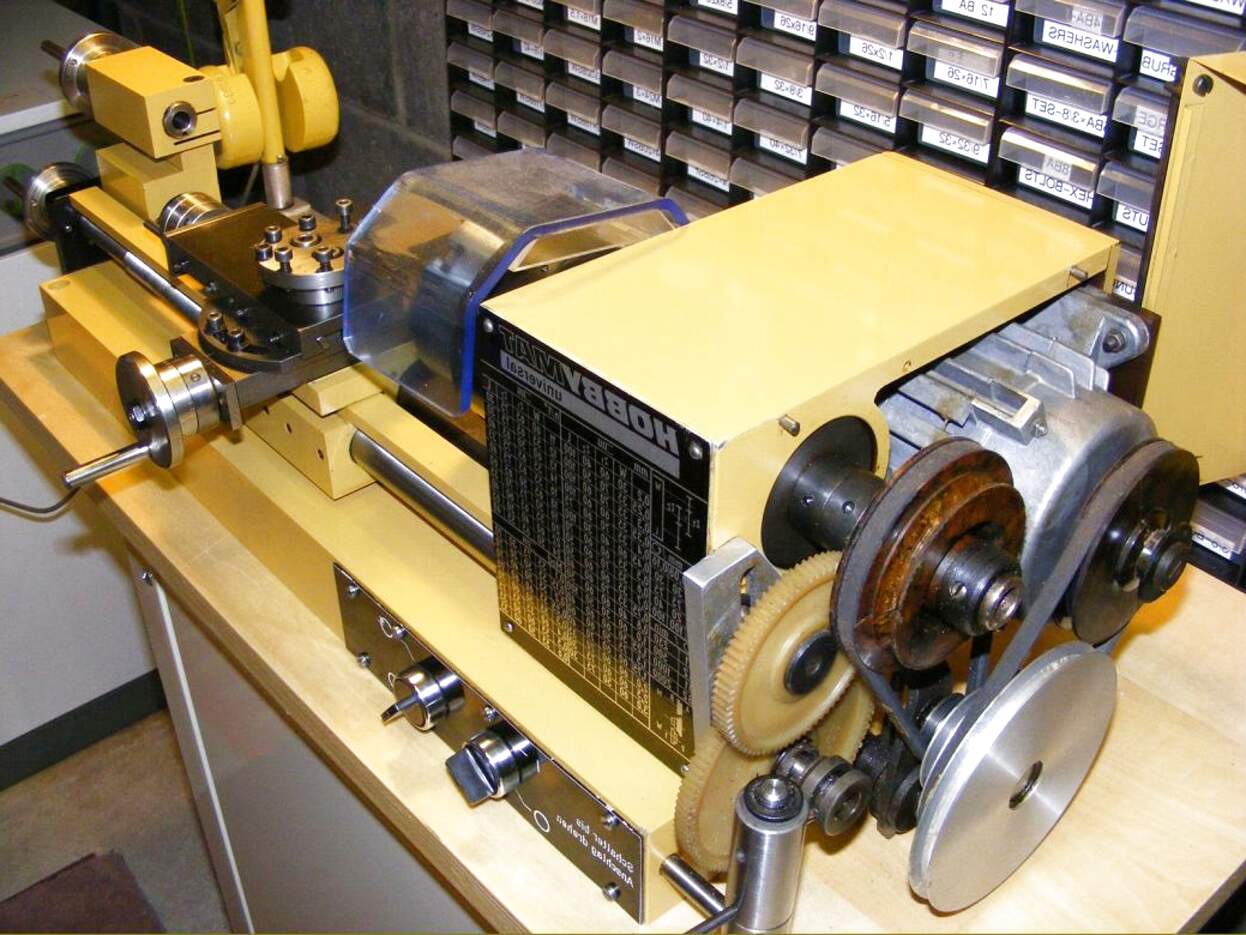
They will take collets in the headstock, most commonly some variant of an 8mm collet (that's the body diameter). They will have a center height between 40 and 70 millimeters, with most being around 50. Watchmaker's lathes are always quite small. Sometimes you have to make a nest or arbor to hold the part for second operations. Just owning the best piece of equipment for the job does not guarantee success. Knowing which cuts to start with, on a complex part, is a good skill too. Also how best to make a precise part- make all the features of the part without removing it from the chuck and then part it off when done. Heck, I don’t know how many times I went onto a machine after someone else and the cutting tip is not on center.
HOBBYMAT UNIVERSAL MD65 LATHE MANUAL MANUALS
If you study basic machining manuals (probably available at the library) you will learn about all this stuff- surface speed, infeed, tool prep based on material, post machine hardening (if needed) and so on. No way I can get the surface speed to properly finish small pivots like that. But I probably could make it pretty decent and would still need a Jacot tool to size and burnish the pivots. I have a very reliable lathe at my disposal but I know better than to try this. 010” oversized so you can file, sand and polish as needed. are all important to make accurate cuts and produce a reasonable surface finish. The shape, sharpness, rake angle, feed (how much does the tip move down the length per revolution) etc. Repeatability (I guess reliability) when using a cross slide- if you dial in 0.001” on diameter, is that what you get? Sloppy ways on a lathe are double jeopardy- you can index (go in) more deeply than the hash marks indicate and also the lathe can “pull” the tool into the work further than intended. I have respect for those who can make these parts by hand I wouldn’t attempt that personally, unless you just wanted to make the part, but not actually fit it to a watch. Traditionally the parts were made by hand, with gravers. 005” diameter when your machine run out is half that. It’s all about tolerance (T.I.R.) and repeatability. You should read up, and now you can watch videos on YouTube to get comfortable.Īnd for simple polishing, you can use a drill or dremel to spin the parts until you are ready.

These are simple, but the motor may not be operating at its most efficient RPM, and larger diameter (slow speed) cuts can stall the motor. Hobby lathes may have a VFD or simple potentiometer resistor to adjust speed. And there may be a high and low range in that pulley or gear set to double the available speeds. But the motor is always spinning at the same RPM. “Real” lathes will have different pulleys and/or gears to set the chuck (or collet) speed.
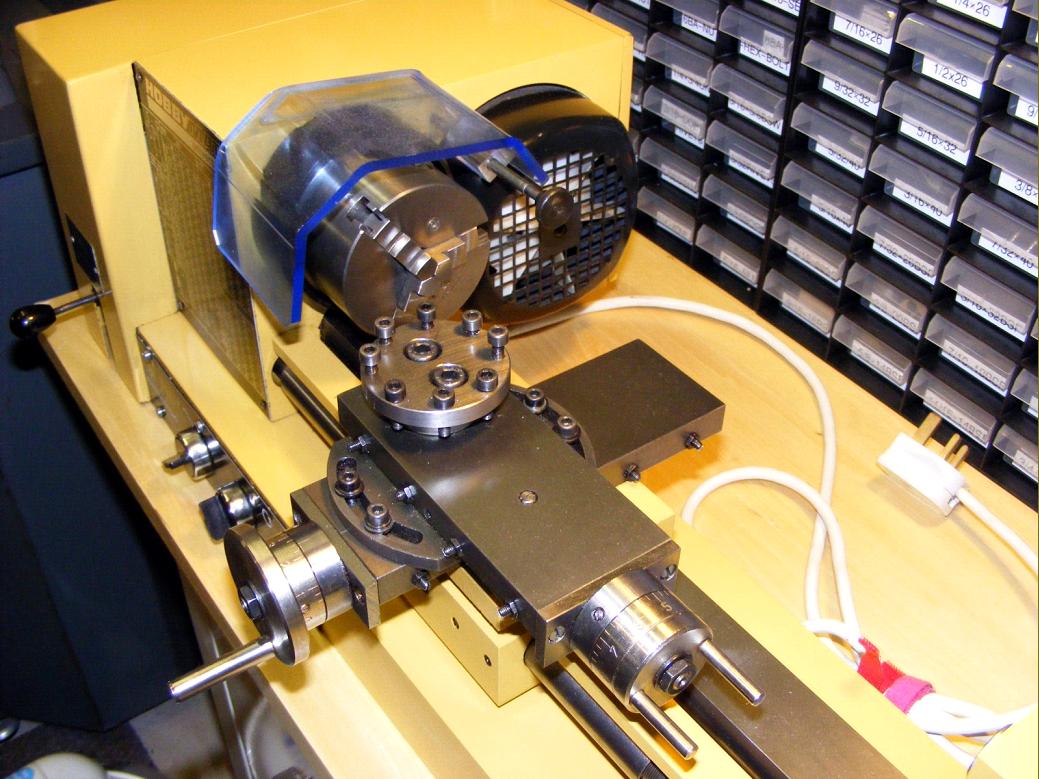
Plenty of charts in machining handbooks. Basically, small diameters spin fast and large ones spin slow. You know the diameter of your work, and you need constant surface speed. You don’t really need “variable speed on the fly” (like with a pedal) with a lathe. The only reason it may matter is it limits collet choices when you want more later, and also the diameter stock that can pass thru the collet. I have also seen 10mm but that seems less popular, along with 6mm. 8mm seems to be the most popular collet size for these lathes.
